FOQ, or Fixed Order Quantity shows us the time and quantity to order inventory. In this article, we will provide you with the Fixed Order Quantity model and formula to help you calculate this metric at ease.
What does Fixed Order Quantity mean?
The Fixed Order Quantity, called FOQ for short, refers to a system of controlling inventory that allows for min and max inventory levels to be fixed. When the inventory level hits the auto-set reorder quantity or the minimum level of stock, the maximum and fixed level of inventory can be replenished.
You are viewing: Which Of The Following Are Fixed Order Quantity Inventory Models
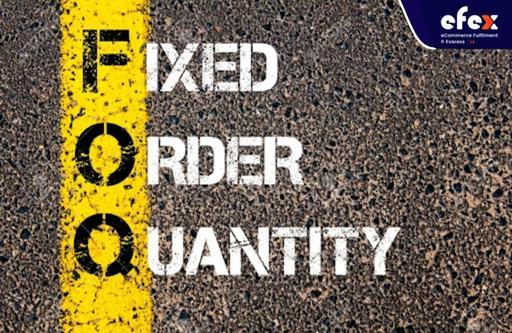
In other terms, a point of auto reorders is connected to the system’s pre-fixed quantity of stock, and as soon as the level of inventory hits the minimum set-point, the point immediately makes a purchase with the provider for the maximum inventory capacity.
The min and max stock levels must be established by the company based on storage capacity as well as demand forecasts. Many businesses utilize the fixed order quantity system because it reduces reorder errors, effectively manages storage space, and avoids wasteful blocking of funds that may be used elsewhere.
This approach also makes sure that inventory items that are presently being implemented in manufacturing get replenished on a regular basis. The Fixed Order Quantity technique makes the assumption that all the variables are well known and constant. Sales, unit costs, holding costs, lead times, stock-out costs, and so on are a few examples of such factors. The strategy is often used by businesses and produces outstanding outcomes, although this assumption could not hold true in real-life scenarios.
👉 Read More: Cumulative Lead Time: Example And Calculation
The Model of Fixed Order Quantity Inventory and Examples
We need to consider how to calculate the order quantity (or Q) and the reorder point (or ROP), these two variables that make up FOQ definition. However, we must first examine the presumptions that this system makes. The system, most critically, presupposes that all variables occur at a constant rate and that their values are proven to be true.
For instance, the system makes the assumption that demand, D, happens consistently and there is no demand variability. Additionally, the holding cost, the lead time, the cost of a stockout, and the unit pricing, are all predictable and set. Even though these hypotheses are unrealistic, the model is quite resilient and still produces outstanding results.
The quantity to order?
The order quantity must be chosen as the first choice in the FOQ model. Remember that there are many expenses associated with inventory, most obviously the holding and order charges. The EOQ indicated earlier is the “optimal” order quantity that we wish to choose because it reduces these costs. This is calculated by finding the order quantity that minimizes the yearly inventory cost.
Read more : Which Leader Supported Pan-arabism In The Mid-twentieth Century
Evaluate the two total annual cost, which is made up of the yearly purchase cost, the yearly ordering cost, as well as the yearly holding cost:
Total cost = Ordering cost + Purchase cost + Holding cost
TC = (D/Q) S + DC + (Q/2) H
- TC: Total cost
- D: Annual demand
- Q: Order quantity
- C: Unit cost
- H: Holding cost
- S: Ordering cost
The first term (D/Q) refers to the yearly ordering expense is S. It is calculated by multiplying the total number of orders made every year (D/Q) by the S cost of every order. The yearly purchase cost of the goods is represented by the second element in the equation (DC). It is calculated by multiplying the unit cost (C) by the yearly demand (D). The average inventory retained is represented by (Q/2) in the third element, which is the yearly holding cost.
Note that once the order is placed, our max inventory is Q units. We have nothing when the inventory is gone. As a result, we typically have Q/2 units in stock. H stands for the inventory holding cost per unit year.
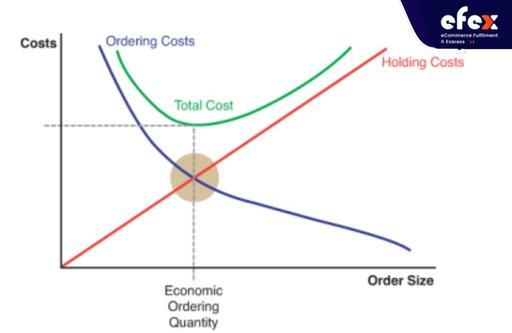
The goal is to choose an order quantity that lowest the overall cost including holding expenses as well as ordering costs and is represented by the lowest value on the overall cost curve. Calculus is used to determine this, leading to the following traditional calculation of the optimal order quantity (EOQ):
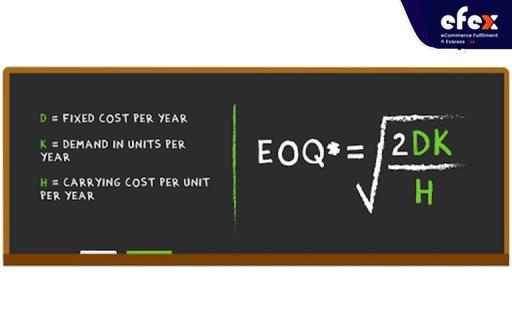
The time to order?
The EOQ provides an answer to the quantity to order, and yet we still need to decide when to place the order. Suppose that the lead time (L) and demand rate (D) are uniform and well-known. In that situation, the ROP would just be sufficient stock to meet the demand for the duration of the lead time. In this straightforward scenario, the ROP would be calculated as
- Demand during Lead Time = ROP
- ROP = D L
Suppose that a product’s lead time (L) is 2 weeks and that its demand (D) is 500 units per week. If the ROP were to
Reorder Point = ROP = D x L = 2 week x 500 = 1000 units
Read more : Which Technique Does The Author Use To Engage The Reader
This implies that an order for the order quantity Q is placed each time inventory hits 500 units. However, D and L are rarely set, and demand is frequently greater than anticipated. We frequently need to carry a little bit more stock, as a result, to account for this unpredictability. This inventory, which we keep on hand besides the demand throughout lead time, is known as safety stock (often known as buffer stock)
👉 Read More: Item Coding: Definition And Benefits
When calculating the ROP, safety stock is also calculated as follows:
- ROP = safety stock + demand during lead time
- ROP = SS + D L
The likelihood that we won’t run out of stock is what is used to calculate safety stock, which is based on the level of service a business intends to keep. The business chooses what quality of service they try to offer for specific goods and customer base when setting this. Greater service levels result in higher inventory levels. The variability of demand is another element taken into account while calculating safety stock.
The bigger the safety stock, or the sum added to the ROP’s final calculation, the greater the variability so the greater the service level.
👉 Read More: Item Master: Example And Best Practices
👉 Read More: 13 Stages Of Procurement Cycle With Detail Instructor
Final Thought
Have you got everything about Fixed Order Quantity? This figure plays an important role in managing inventory. The specific recommendations made for the most economical quantity of units per order are the EOQ model’s key benefit. To benefit from bulk purchasing discounts and reduce purchase costs, the model may advise purchasing a bigger quantity in fewer orders.
Applying the Fixed Order Quantity model probably will truly benefit your business. Therefore, remember to learn it as deeply as possible. Hope you have a good time with Efex.
Source: https://t-tees.com
Category: WHICH