2.9K
With any device or piece of equipment that exists, there is likely a specification sheet that comes with it.
You are viewing: What Is A Cut Sheet In Construction
If you’ve ever purchased a computer before then you likely went and looked at what the specs are for the machine as well. This is no different for construction, but it can be referred to by many different things, one being the cut sheet.
I might throw around some different terms for cut sheets in this article. This is just to get you familiar with how it might be named. You will also see the terms product data sheet or just data sheet.
What is a cut sheet and how it’s used in construction? What do you do with a cut sheet?
With a cut sheet, the main objective is to give people information about the equipment. For example, if I am looking at the flow capacity of a fan coil unit, then I need to refer to the spec sheet to find this. You can also find the product description and advanced features to give you an overview of the equipment capabilities.
You can gather the power requirements, dimensions, weight, features, etc.. But it’s important is that you understand what’s required per the contract specifications, this way you can select the right equipment.
Here’s a quick application of a cut sheet:
Many engineers will perform a design with a certain brand of equipment in mind. They can use a cut sheet to tell them what they can expect from some equipment to meet the building demands.
When you look at an equipment schedule in the contract drawings, the comments section will show model numbers listed. There will be a note that says something along the lines of “model number or approved equal”. This is saying that you can either choose to use the part specified or choose something similar.
You would then look to other vendors or manufacturers to see if they can provide any equipment with similar specs. They will provide you with their cut sheet where you can compare the different equipment. If it appears to line up, then you might be able to use the similar model for the project.
The advantage here is that you might be able to get a lower price by using a similar model. This can either make your price more competitive during bid or increase your margin after the job has been awarded.
If you’re in the bidding phase of a job, then I advise that you get a price for the equipment that was spec’d out. The last thing you want is to submit the equipment with the lower price and the engineer rejects it. Then you will have to pay more out of pocket to cover that cost.
Common Use Case for Cut Sheets:
Submittals
As the heading might suggest, a submittal is a document that you submit to the design engineer. The submittal will contain the cut sheet for the equipment you will be planning to use for the project. The project engineers or managers will be responsible for sending in this document for review.
The design engineer will then take this document and review it. During the review process, they will look to see that the specification sheet lines up with what they selected. If they find that your selection is good, then they will provide you a formal response with an approval.
When the equipment submittal has been approved you can proceed to ordering. Then you wait for the equipment to arrive.
Read more : What Are The Problems With All On 4 Dental Implants
I just want to note that construction submittals are not just limited to cut sheets. The documents that you have to submit are based on what is required per the project specifications.
Selection for Supporting Equipment
When you order a large piece of equipment you typically don’t just order the one part and call it a day. There’s other parts that you will need to order that will allow the equipment to function properly.
Let’s take an air handling unit for example. You look at the technical documents and looking at the power requirements tells you with some important info.
A constant volume air handler will require a starter, but a varying speed will required a variable frequency drive (VFD) to run the fan motor. You can’t just order any VFD or starter of your choice. You need to make sure these devices have the correct capacity to safely operate your equipment.
Without the correct VFD or starter you will not having a working fan motor. This will create some major issues on and construction projects. Not only will the cost for the replacement be required, but now there’s a delay in the schedule.
Now, you will need to make sure that you can properly support the equipment. Dive into the specifications and look for the dimensions and weight. You should be able to develop a plan for creating a supporting member for your piece of equipment.
Some manufacturers might also require that you provide vibration isolators. To learn more about vibration isolators, check out the link below to see why they’re important.
This is just one example of how you can use a cut sheet to make selections on supporting equipment.
Field Equipment Verification
As your equipment arrives to the field, the first thing you should be doing is check to make sure you have the right parts. You will do so by referring to the product sheets, looking for the model number, checking dimensions, etc.
Using the AHU example again, you might need to refer to the cut sheet to determine how to assemble the unit properly. This would be found in the certified drawing section of the individual sheets.
The shop drawings can also tell you how the equipment should be wired. Verifying something is wired correctly, especially a fan motor is important. If it’s wrong, you could have a fan that’s running backward!
Cut Sheet Examples and How to Review
We touched on the submittal process and what’s required when you submit a cut sheet. But let’s discuss what you need to look for when you prepare a submittal.
As you review the construction plans, you will need to look for the equipment schedule sections. For this particular example, we will be looking at the mechanical plans.
The equipment schedule will look something like the image seen below.
Read more : What Can I Use Instead Of Gloves
As you can see, there’s a lot of information to digest here. The good news is that there’s only a few columns that you have to really pay attention to.
The best way to make sure you meet the specified equipment is to order the model that was selected in the schedule. If you’re able to find a vendor that sells the exact model then you’re in luck!
Your vendor can provide you with the equipment submittal. This should contain some mark ups which let you know what product they’re selecting. See below for an example.
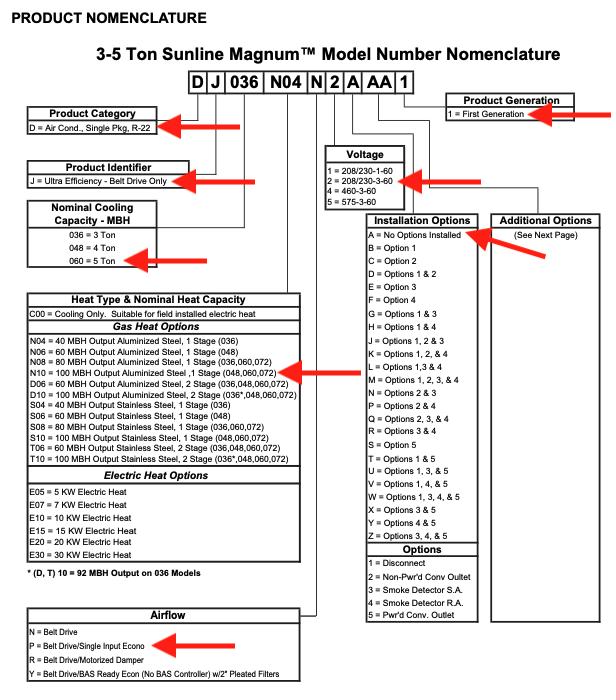
But if not, then you will need to find something that’s comparable.
Sometimes a design engineer will select equipment based on the specifications of a particular product. If the product is discontinued or the lead time will impact the schedule deadline, then an alternative will need to be proposed. In construction, this is considered a variance.
If this happens and the price of the alternative equipment is higher then you’re entitled to a change order. To learn more about change orders, check out my article on it.
You’ve selected your alternative. Now, as you’re reviewing the cut sheets, you need look at the electrical, tonnage, refrigerant, heating data, etc… This needs to line up with what is shown in the equipment schedule.
If your proposed alternate does not meet these requirements, then chances are your variance will get rejected. The engineer may compromise and allow the equipment should they feel it will meet the project demands. This is why it needs to go through the review process.
The link for the equipment cut sheet can be found below if you would like to review this document. There’s a lot of information here, you don’t need to use everything when you’re putting together a variance submittal. Just be mindful of the critical items, which is typically included in the equipment schedule.
Conclusion
You should now understand cut sheets a bit more and how they relate to the construction field. At first it may not make sense why they’re so important, but the information they provide is what makes it so valuable.
Get familiar with what you should be looking for when referencing a cut sheet. That way you can produce submittals without burning up too many hours.
It’s also good to understand what to look for because you’ll be referring back to the cut sheets throughout the project. You don’t want to hunt down the individual sheets every time you open up the document.
With some experience, you’ll quickly see why cut sheets play such a vital role in a construction project.
Thank you for reading.
Source: https://t-tees.com
Category: WHAT